An Alternative Process to Manufacture pMDIs, for a Smooth Transition to Low Global Warming Potential Inhalers
Innovation PitchDrug Delivery SystemsInhalersPharmaceuticalsSustainability
2025-06-05 | 10:40 AM - 11:00 AM | The Innovation Corner
Information
Kris Brosig1, Irene Rossi1, Sally Stanford2, Sheryl Johnson2, James Murray2, Tony Clark3, Marco Laackmann1
1Harro Höfliger, Helmholtzstraβe 4, Allmersbach im Tal, 71573, Germany
2Orbia Fluor & Energy Materials, Thornton Science Park, Pool Lane, Ince, Cheshire, CH2 4NU, United Kingdom
3Pharmatec Solutions, Timberly, Cinders Lane, Gyfelia, LL13 0YH, United Kingdom
3Pharmatec Solutions, Timberly, Cinders Lane, Gyfelia, LL13 0YH, United Kingdom
The Kigali Amendment to the Montreal Protocol aims to reduce carbon emissions by targeting high global warming potential propellants, such as those in refrigerators and, consequently, in pressurized metered dose inhalers (pMDIs). Two low GWP (LGWP) propellants have been identified [1], with 1,1-difluoroethane (HFA 152a) reducing the carbon footprint of pMDIs by over 90% compared to current HFA-134a formulations [2]. However, HFA 152a is extremely flammable, forcing pMDI manufacturers to put additional safety considerations and measures in place, adding more challenges to traditional manufacturing processes, such as single-stage or two-stage filling [3].
During the mixing and filling process of the formulation, which includes drug, excipients, and propellant, safety becomes then a critical concern with specific ATEX ("ATmosphères EXplosibles") areas to be designed and implemented requiring pharmaceutical companies, in certain cases, to build entire new facilities. By decoupling the filling of individual ingredients and applying direct active pharmaceutical ingredient (API) filling into the canister, these challenges can be mitigated. This method allows the use of existing facilities with less stringent ATEX requirements, eliminating the need for large volume mixing vessels and enabling bulk storage of propellants outside the facility. This significantly reduces the risks associated with handling HFA 152a.
The direct API filling approach uses proven powder filling technology, involving the direct dosing of fine micronized API into the aluminum canister, crimping the valve, and subsequently filling the pMDI with the propellant. This method enhances manufacturing efficiency and is adaptable to continuous batch production.
To assess this concept, we have tested the adaptability of a dry powder filling equipment for pMDIs manufacturing at bench scale. The use of this technology to dispense pure API into a canister resulted in dosing within ±10% of the target fill weight. Optimized trial dosages were within 6% of the target weight, with low relative standard deviation values of 1.7-2.1%. In-vitro stability studies of salbutamol sulphate and pharmaceutical performance testing were conducted, along with the assessment of the impact of vacuum crimping on dry powder-filled canisters. These findings suggest that dry powder filling technology is a viable option for pMDIs manufacturing, demonstrating good precision, accuracy, and product stability.
- Wang H, Leal J, Ordoubadi M, Minootan Z, Lachacz K, Carrigy N, Lechuga-Ballesteros D & Vehring V: Understanding the performance of pressurized metered dose inhalers formulated with low Global warming potential propellants. Aerosol Sci Technol 2024, 58(2): 115-133.
- Stanford S, Johnson S and Robinson I: An assessment of the effect of vacuum crimping on dry powder filled pMDI cans. In Respiratory Drug Delivery 2024. Edited by Dalby RN,Peart J, Suman JD, Young PM, Traini D, Watts A. RDD Online; Richmond, VA: 2024: 304–307.
- Attkinson, N.: Considerations for Robust Clinical and Commerical Manufacturing of Next Generation Sustainable Metered Dose Inhalers. Respiratory Drug Delivery 2022.
Exhibitors
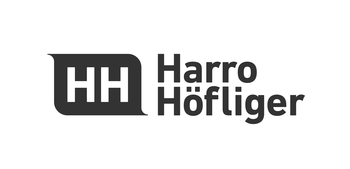